バンニング・デバンニング作業とは?倉庫設計時に考えるべき理由を解説
投稿日:2023.12.22
更新日:2024.01.09
お役立ち情報
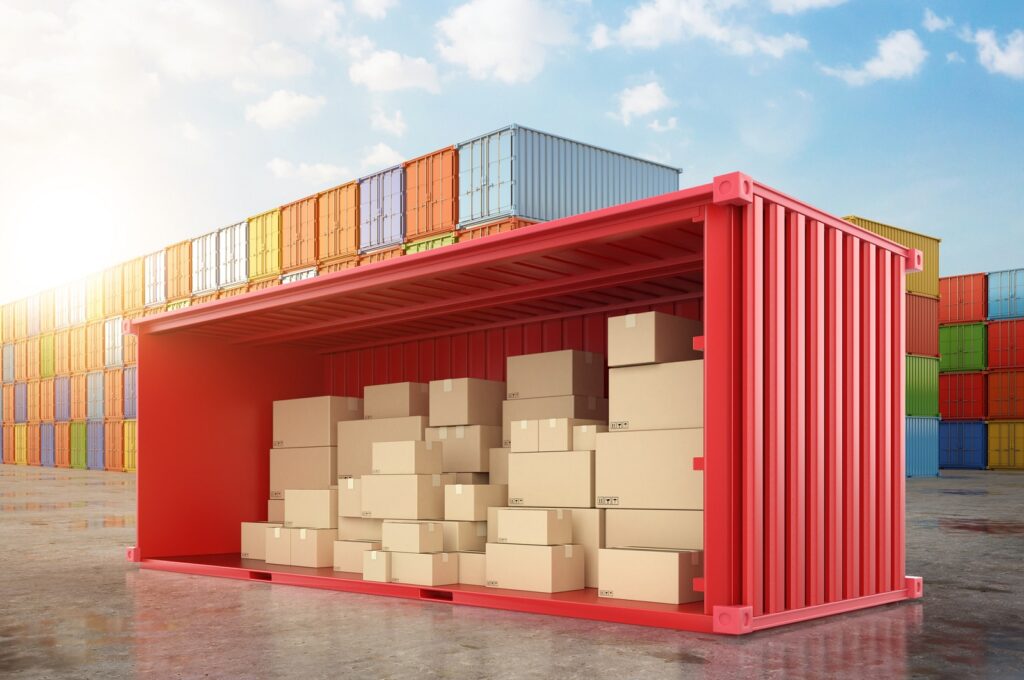
バンニング・デバンニング作業とは、コンテナ輸送に関係する作業を表す物流用語なのですが、物流業界で働いている方でも「バンニング」「デバンニング」がどのような作業を指しているのかはっきりとは分からないという方も少なくないと思います。
そこで、ここではバンニングとは?デバンニングとは何か?を解説したうえで、この作業に関わる倉庫を建設する際に注意すべきポイントをまとめてみます。
Contents
バンニング・デバンニング作業とは?
それでは、貿易用語の「バンニング」「デバンニング」作業について、どのような作業を指しているのかについて解説します。バンニング・デバンニング作業は、それぞれ以下のような作業を指しています。
- バンニング(Vanning)作業
貨物をコンテナに積み込む作業のことを指しています。バンニングは、英語で書くと「Vanning」となります。「Van」には「貨物をコンテナに積み込む」という意味があり、これを動名詞化したものとされています。なお、物流業界では、単に「バン」と呼んだり「バン詰め」と呼ぶこともあるようです。 - デバンニング(Devannng)作業
デバニングは、コンテナに入っている貨物を取り出す作業を指しています。英語で書いたときには「Vanning」の前に「de」が入るのですが、英語の接頭辞deは、否定の意味合いを持っており、バニングの逆の意味を持っていると考えてください。
バンニング・デバンニング作業は、上記の通り、コンテナへの貨物の積み込みと貨物の取り出しを意味しています。ここで注意しておきたいのは、コンテナ輸送を行う際の運賃は、「コンテナ単位」で決まるという点です。簡単に言うと、コンテナ内にぎっしりと荷物が埋まっていようと、スカスカの状態だろうと、コンテナ1本にかかる運送コストは変わらないということです。
したがって、バニング作業では、コンテナのスペースを可能な限り有効活用できるように貨物の積み込みを行うことがポイントとなります。なお、輸送中の揺れなどにより、コンテナ内の荷物が荷崩れしないよう、緩衝材などを利用してしっかりと固定する、貨物の重量バランスを考慮することも、バニング作業を行う上で重要とされてます。
バンニング作業のポイント
バニング作業を行う時には、以下のような点に注意する必要があるとされています。
- 効率よくコンテナ内に貨物を積み込む
上述したように、コンテナ輸送は、コンテナの中にどれほどの貨物が入っているのか関係なく、コンテナ単位で輸送費が決まります。したがって、一度に多くの貨物が運べるよう、効率よく積み込むテクニックが重要とされています。 - 揺れなどで荷崩れを起こさないようにする
海上輸送では、波で船が揺られ、コンテナ内の荷物が荷崩れを起こす恐れがあります。したがって、バニング作業時には、コンテナ内の貨物を確実に固定することが大切です。 - デバンニングしやすくするために配慮する
輸送先では、コンテナから貨物を取り出すデバニング作業が必ず行われます。揺れなどで、貨物が取り出しにくくなっている、バランスが悪くなっているなんてことになると、デバニング作業中に貨物が崩れて、作業者にあたってしまうなど事故の可能性があるので、安全に作業ができるように貨物の積み込みを行うという配慮も必要です。
バニング作業は、コンテナ内のスペースを可能な限り使用することでコスト削減が実現しますが、デバニング時の作業のしやすさ、安全性のことも考慮しなければいけません。実は、バニング作業を効率的、バランスよく作業するには、倉庫建設時のレイアウト設計が非常に重要です。次項でその辺りのポイントについて解説します。
倉庫のレイアウト設計が重要
倉庫建設時に倉庫のレイアウト設計が重要なのは、業務効率化やコスト削減などに大きく貢献できるからです。事業用倉庫の多くは、保管や出荷という役割で使われるわけですので、保管であれば空間を無駄に使わずに多くの荷物を配置できる間取りにする、また保管した荷物をできるだけ効率よく出荷できる動線を意識します。
これは、一般的に「動線設計」と呼ばれ、倉庫建設時においては非常に重要なポイントになります。例えば、保管のことばかりを考えて、ギチギチに荷物の積み込みを行った場合、搬出や積み込みがしにくい空間となり、荷物の出荷に時間がかかるなど、作業効率が大幅に落ちてしまうことでしょう。作業効率の低下は、物流コストの増加にも直結します。
それでは、保管と出荷のどちらも考慮した倉庫を作るためには、どのような点に注意すべきなのでしょうか?以下で、倉庫のレイアウト設計を決める際の注意点を解説します。
全体のレイアウトを設計する
倉庫のレイアウト設計を決める時には、まず保管する荷物の配置を大まかに決めてから、細かな配置を決めていくという流れで進みます。どのエリアに、どのような特徴を持つ商品を配置するのか、ざっくりと決めていきましょう。
例えば、出荷頻度が高い荷物は「メイン動線(主に使う移動経路)」上に配置して、その逆に出荷頻度が高くない商品はメイン動線から遠ざけて配置するといった感じです。大まかにでも、倉庫全体のレイアウトが決まれば、次に紹介するメイン動線との関係性が分かりやすくなります。
移動動線をレイアウトにのせる
全体的なレイアウトが決定したら、倉庫内作業の一連の流れを当てはめ、倉庫内での移動動線を明確にしていきます。一般的な倉庫では、「入荷⇒検品⇒入庫⇒保管⇒出庫⇒梱包⇒出荷」と言った流れで荷物が移動します。この一連の流れを、上で決定したレイアウト図面にのせていき、動線が一筆書きで完結するのかを確認しましょう。一筆書きで完結する動線になっていれば、無駄のないレイアウトになっていると判断できます。
一方、移動動線が倉庫内を行ったり来たりしているようであれば、非効率な動線になっていると判断できるため、全体のレイアウト設計を見直す必要があります。倉庫建設時には、全体のレイアウトを決めたのち、実際の移動動線を具体化することで、より作業効率の良い倉庫のレイアウトを導き出す必要があります。
マテハン機器の乗り入れも考慮しなければならない
倉庫設計時にありがちなミスが、人の作業動線ばかりに注目して、フォークリフトなどのマテハン機器の乗り入れや作業スペースを考慮していないレイアウトになってしまうというものです。
例えは、倉庫内の通路幅が人にとっては十分だけど、マテハン機器を乗り入れた時にはギリギリの幅で「曲がれない」「曲がりにくい」といったレイアウトになると、マテハン機器の良さを生かすことができず、作業効率を低下させる要因になります。特に、バニング・デバニング作業が前提となる倉庫などでは、マテハン機器が単に入るだけでなく、最も効率よく稼働できる動線や間取りにすることが大切です。
なかでも危険物倉庫の場合は、その設置基準(高さ制限)から低床となる事が多く、バンニング・デバンニング作業の方法については初期段階での計画が必須となります。”複数棟の計画であれば1棟は高床とする”、”危険物倉庫は低床とし別途バンニング・デバンニング用の建屋を計画する”、”リーチスタッカーのような特殊搬送車両を導入する”など、敷地全体の配置計画時に十分に検討しておく必要があります。
倉庫建設では、入庫から出荷まで、幅広い荷役作業を効率よく行える施設を作ることが非常に大きなウェイトを占めています。荷役にもさまざまな種類がありますが、どこか一つの作業が滞るだけでも大きなタイムロスが生じ、生産性が低下するリスクがあります。そして、その他の作業にも悪影響をおよぼし、混乱が生じることで物流コストの増加につながる恐れがあります。
したがって、倉庫を建設する際には、入庫から出荷までの作業を可能な限りスムーズに行えるような環境を整えられるレイアウト計画を行わなければならないと考えてください。
最適な倉庫レイアウトを実現するため、非常に重要な要素となると言われる物流分析について詳しく解説しています。
まとめ
今回は、物流業界で用いられている「バニング」「デバニング」作業の意味と、バニング・デバニング作業のことも考慮した倉庫を建設する際の注意点を解説しました。
記事内でご紹介したように、バニング・デバニングは、貿易に関わる物流用語で、コンテナへの貨物の積み込み、取り出し作業のことを意味しています。コンテナ輸送は、大量の荷物をまとめて輸送することができるため、航空輸送などと比較すると、輸送にかかるコストを削減することができます。
ただ、コンテナ輸送にかかるコストは、コンテナ単位で決まりますので、コンテナの中に効率よく貨物を積み込むことが大切です。したがって、バニング・デバニング作業を考慮した倉庫を建設する際には、人だけでなくフォークリフトなどのマテハン機器もスムーズに稼働できるレイアウト計画が必要です。
関連記事
ARCHIVE
TAG
- #建設準備
- #グラフ
- #建築費
- #ドライバー不足
- #立地
- #2024年問題
- #3PL
- #3温度帯
- #4温度帯
- #AGV
- #AI
- #AVG
- #CAS冷凍
- #EC
- #FSSC22000
- #GDPガイドライン
- #IoT
- #IT
- #LED
- #RiSOKOセミナー
- #Society 5.0
- #Third Party Logistics
- #エアコン
- #カーボンニュートラル
- #ガソリン
- #グッズ
- #コールドチェーン
- #コロナ
- #コロナ禍
- #システム建築
- #タグを削除: RiSOKOセミナー RiSOKOセミナー
- #デバンニング
- #トラック待機時間
- #バンニング
- #ひさし
- #ピッキング
- #フォークリフト
- #プラスチック削減
- #フルフィルメント
- #プロトン凍結
- #フロン排出抑制法
- #フロン管理義務
- #マテハン
- #マテハン機器
- #メディカル物流
- #ラック
- #リチウムイオン蓄電池
- #ロボット
- #ロボット化
- #中小企業支援策
- #事故事例
- #人手不足
- #人材不足
- #低温倉庫
- #低温物流
- #保安距離
- #保有空地
- #保管効率
- #保管場所
- #保管温度帯
- #倉庫
- #倉庫の強度
- #倉庫の種類
- #倉庫建設
- #倉庫建設コンサルタント
- #倉庫新築
- #倉庫業法
- #倉庫火災
- #免震
- #共同物流
- #冷凍倉庫
- #冷凍自動倉庫
- #冷凍食品
- #冷蔵倉庫
- #冷蔵庫
- #削減
- #労働時間
- #労働災害
- #医療機器
- #医療物流
- #医薬品
- #医薬品の物流業務
- #医薬品保管
- #医薬品倉庫
- #危険物
- #危険物倉庫
- #危険物施設
- #営業倉庫
- #国際規格
- #土地
- #地震
- #地震対策
- #基礎知識
- #安全
- #安全対策
- #定期点検
- #定義
- #対策
- #屋内タンク貯蔵所
- #屋内貯蔵所
- #工場
- #工場の衛生管理
- #建築基準法施行令
- #建設計画
- #従業員
- #感染予防
- #技術
- #換気設備
- #改修工事
- #政令
- #新型コロナウイルス
- #新築
- #施設設備基準
- #機能倉庫建設
- #水害
- #水害対策
- #治験薬
- #法律
- #消防法
- #消防設備
- #温度管理
- #火災
- #火災対策
- #災害
- #無人搬送ロボット
- #無人搬送車
- #無人配送車
- #燃料費
- #物流
- #物流DX
- #物流センター
- #物流倉庫
- #物流倉庫新設
- #物流倉庫自動化
- #物流拠点
- #物流業界
- #物流総合効率化法
- #物流課題
- #特殊倉庫
- #用途地域
- #異物混入
- #着工床面積
- #空調
- #結露
- #耐震工事
- #職場認証制度
- #自動倉庫
- #自動化
- #自動車運送事業者
- #衛生管理
- #補助金
- #規制緩和
- #調理器具
- #貸倉庫
- #軽油
- #適正流通ガイドライン
- #関西物流展
- #防災
- #防災用品
- #防爆構造
- #集中豪雨
- #電気代
- #電気代削減方法
- #静電気
- #静電気対策
- #非危険物
- #非接触
- #食品倉庫
- #食品物流
- #食品衛生法
もっと見る▼