今さら聞けない倉庫の基礎知識。物流業界で耳にする『ピッキング』とは?
投稿日:2020.07.08 お役立ち情報
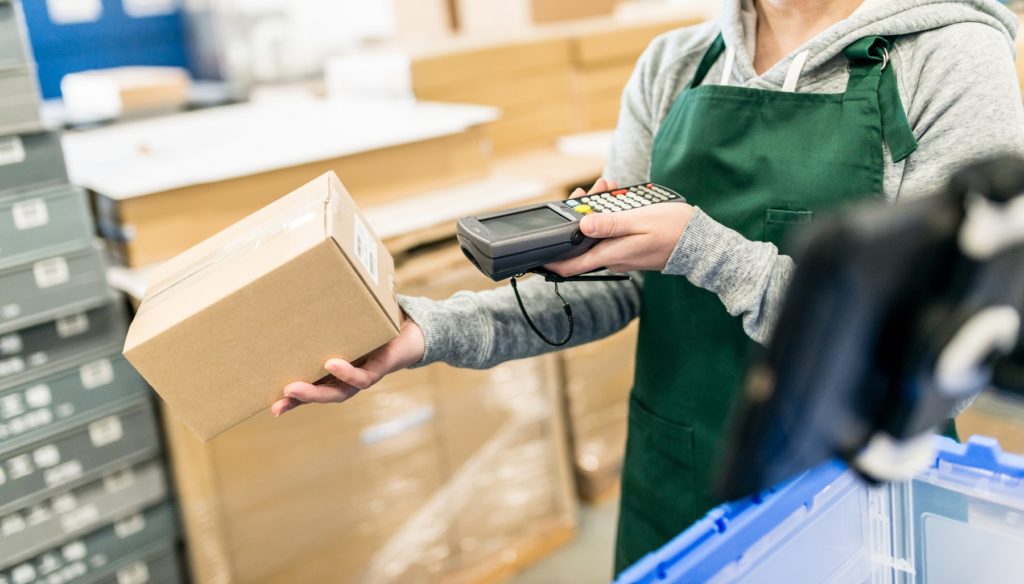
今回は、物流倉庫などで必要不可欠となる『ピッキング』の基礎知識についてご紹介していきたいと思います。現在、物流業界で働いている方であれば、「ピッキング」という言葉を一度は耳にしたことがあると思いますし、ピッキングが何を指しているのかについてはある程度理解していると思います。
しかし、一口にピッキング作業と言っても、使用する機材やピッキングの方式にはいくつかの種類が存在しており、それぞれの強みは異なるのです。一昔前であれば、指示書や伝票に沿って人間が倉庫内を歩き回って必要な商品をかき集めてくるというのがピッキングの常識でしたが、さまざまな技術が進化した現在では、より正確で効率的なピッキング作業が求められるようになっているのです。
そこで今回は、物流業界で働く方がおさえておきたいピッキングの基礎知識について簡単に解説していきます。
Contents
ピッキングの意味は?
まずは、ピッキングの基礎知識として、ピッキングという言葉がどのような作業を指しているのかを簡単にご紹介しておきます。ピッキングは、物流倉庫などで出荷指示書(ピッキングリスト)に従って、一時的に保管されている場所から商品をピックする(拾い集める)作業のことを指しています。似たような言葉として「仕分け」というものもあるのですが、こちらは「1か所にあるものを分けて置いていく」という意味で使われることが多く、商品を拾い集める作業であるピッキングとは異なる意味で使われることが多いです。
物流倉庫などの出荷作業は、「保管されている商品をピッキングリストに沿って出荷場所に集める⇒集めた商品を仕分ける⇒梱包して送付状を貼る⇒納品先別に仕分けする⇒トラックに積み込む」などと言った工程で進められるものです。ピッキングの時点で間違いが発生した場合には、その後の工程全てが崩れてしまうことになりますので、何よりも正確性が求められる作業と言えるでしょう。
ピッキングに関しては、上記のような物流倉庫で必要になる作業と考えられがちです。しかし、さまざまな製品の製造を行う工場などでも、使用する部品を集めるなどと言った作業はあるでしょうし、どんな会社でも大なり小なりピッキング作業は行っているものです。
ピッキングにも種類がある
保管場所にある商品や、一時的に保管された場所から商品を集めるのがピッキング作業ですが、ピッキングにも「摘み取り方式」と呼ばれるものと、「種まき方式」の大きく2種類に分けることができます。以下でそれぞれの方式の特徴を簡単にご紹介しておきます。
摘み取り方式
摘み取り方式は、商品が保管された棚の前を、作業者が台車やカートなどを押しながら往復し、ピッキングリストに記載されたものを集めていくという方式で、畑に育った野菜を「摘み取る」姿になぞられてこの名称がつけられています。ちなみに、この方式は別名で「シングルピッキング」、「オーダーピッキング」などとも呼ばれます。
摘み取り方式のメリットは、商品を集めて梱包、出荷までの工程がスピーディーに進むことや小回りが利くことです。そのため、発送先が多く、多種多様な商品の出荷が必要になる通販関連の物流倉庫で採用されることが多いです。デメリットとしては、ピッキングを行う作業者は倉庫内を何度も移動しなければならず、移動距離が多くなり労力がかかることです。
種まき方式
種まき方式は、あらかじめ商品をピッキングしておき、荷さばき場で発送先別に仕分ける方式となります。荷さばき場に、出荷先・運搬先が決められた台車やかごが置いておき、手元にある商品をかごに配って歩く方式で、畑で種をまく姿になぞらえて「種まき方式」と呼ぶのです。ちなみに、「トータルピッキング」や「アソート式」などとも呼ばれます。
種まき方式は、複数の出荷先の商品をまとめて取りに行く方式となるため、作業者が何度も商品を取りに行くことがなくなり、移動距離や時間を短縮できるというメリットがあります。デメリットとしては、荷さばきのためのスペースを確保する必要があることや、商品の追加などがあったとしても、仕分け状況が把握しにくく、対応に手間がかかることです。
上記の2つの方式に関しては、どちらが優れていて、どちらが劣っている…というものではありませんので注意しましょう。一般的に、どちらの方式を採用するのかは、取扱商品の『アイテム数』と『出荷先の数』との関係で自社に見合った方式を選定することになります。
ITを活用したピッキング方法
■ストックフォト用にレンタルした施設にて撮影を行っています。
従来のピッキングは、「リストピッキング」などと呼ばれる方法で、作業者がピッキングリストに記載されている商品を確認し、目視で保管スペースから探し出すという方法がとられていました。しかし、この方法によるピッキングは、作業者が手作業で商品の確認を行うことになりますので、正確性が低くミスが発生しやすくなってしまいます。そこで近年では、ピッキングの際の人為的ミスの削減や作業効率の向上のため、さまざまなIT技術が活用されるようになっています。
ここでは、代表的なITを活用したピッキングシステムをいくつかご紹介していきます。
バーコードやQRコード
バーコード・QRコード方式は、商品にバーコードやQRコードを貼りつけておき、作業者が手にしたハンディターミナルなどのバーコードリーダーで読み込むという方法です。この方法の場合、ピッキングリストに記載されている商品と異なるものを読み込むと、エラー音やバイブなどで知らせてくれるため、ピッキングミスの減少や作業効率の向上が期待できます。
バーコード・QRコード方式は、比較的簡単に導入できますので、現在この方法を使っている企業は多いです。
RFID
RFIDは「Radio Frequency Identifier」の略で、RFIDタグを使ったピッキング方法となります。この方法は、作業者が専用の無線通信を行う機械を使ってRFIDタグの情報を読み込むというもので、上述のバーコード方式と同様にミスを少なくして正確なピッキングが行えるようになります。
RFIDは、バーコードなどよりも幅広い情報を読み取ることができるようになるため、出荷する商品のピックアップが効率的になると言われています。RFIDの詳細については、弊社が運営するオウンドメディア『Fact ism(ファクトイズム)』内の記事でご紹介していますので、以下の記事もご参照ください。
参考記事:『レジ待ち』を解消すると言われるRFIDって何だ?RFIDの基礎知識と活用事例について
デジタルピッキングシステム(DPS)
デジタルピッキングシステムは、商品が保管されている棚にデジタル表示器を取り付け、表示機の指示に従って商品を集めていくピッキングシステムになります。
DPSの場合、表示機の指示通りにピッキングを行っていけば良いだけですので、商品知識が少ない新人でも作業に支障がなく、ピッキングミスの減少、作業スピードの向上など、さまざまなメリットがあると言われています。
まとめ
今回は、物流倉庫などでは必要不可欠な作業となるピッキングの基礎知識についてご紹介してきました。一昔前であれば、倉庫内を作業者が何度も往復し、人の目で商品の種類や数量を確認するというのがピッキングの当たり前でした。しかし最近では、できるだけ人為的ミスがなくなるようにピッキング作業にもさまざまなIT技術が活用されるようになっています。
さらにそれを進化させたものが自動倉庫であり、自動倉庫の場合商品の入荷から出荷までを全てロボットが行うようになると想定されています。日本国内では、生産現場への自動化が先行しているようなイメージですが、今後物流業界へもどんどん自動化の波がやってくることでしょう。もちろん、倉庫に新たな技術や設備を導入する場合にはそれなりのコストがかかってしまいますので、まずは自社の課題がどこにあるのか、どういったシステム・機械であればそれが解消できるのかと言う点を検討するところからスタートしてみてはいかがでしょうか。
関連記事
ARCHIVE
TAG
- #建設準備
- #グラフ
- #建築費
- #ドライバー不足
- #立地
- #2024年問題
- #3PL
- #3温度帯
- #4温度帯
- #AGV
- #AI
- #AVG
- #CAS冷凍
- #EC
- #FSSC22000
- #GDPガイドライン
- #IoT
- #IT
- #LED
- #RiSOKOセミナー
- #Society 5.0
- #Third Party Logistics
- #エアコン
- #カーボンニュートラル
- #ガソリン
- #グッズ
- #コールドチェーン
- #コロナ
- #コロナ禍
- #システム建築
- #タグを削除: RiSOKOセミナー RiSOKOセミナー
- #デバンニング
- #トラック待機時間
- #バンニング
- #ひさし
- #ピッキング
- #フォークリフト
- #プラスチック削減
- #フルフィルメント
- #プロトン凍結
- #フロン排出抑制法
- #フロン管理義務
- #マテハン
- #マテハン機器
- #メディカル物流
- #ラック
- #リチウムイオン蓄電池
- #ロボット
- #ロボット化
- #中小企業支援策
- #事故事例
- #人手不足
- #人材不足
- #低温倉庫
- #低温物流
- #保安距離
- #保有空地
- #保管効率
- #保管場所
- #保管温度帯
- #倉庫
- #倉庫の強度
- #倉庫の種類
- #倉庫建設
- #倉庫建設コンサルタント
- #倉庫新築
- #倉庫業法
- #倉庫火災
- #免震
- #共同物流
- #冷凍倉庫
- #冷凍自動倉庫
- #冷凍食品
- #冷蔵倉庫
- #冷蔵庫
- #削減
- #労働時間
- #労働災害
- #医療機器
- #医療物流
- #医薬品
- #医薬品の物流業務
- #医薬品保管
- #医薬品倉庫
- #危険物
- #危険物倉庫
- #危険物施設
- #営業倉庫
- #国際規格
- #土地
- #地震
- #地震対策
- #基礎知識
- #安全
- #安全対策
- #定期点検
- #定義
- #対策
- #屋内タンク貯蔵所
- #屋内貯蔵所
- #工場
- #工場の衛生管理
- #建築基準法施行令
- #建設計画
- #従業員
- #感染予防
- #技術
- #換気設備
- #改修工事
- #政令
- #新型コロナウイルス
- #新築
- #施設設備基準
- #機能倉庫建設
- #水害
- #水害対策
- #治験薬
- #法律
- #消防法
- #消防設備
- #温度管理
- #火災
- #火災対策
- #災害
- #無人搬送ロボット
- #無人搬送車
- #無人配送車
- #燃料費
- #物流
- #物流DX
- #物流センター
- #物流倉庫
- #物流倉庫新設
- #物流倉庫自動化
- #物流拠点
- #物流業界
- #物流総合効率化法
- #物流課題
- #特殊倉庫
- #用途地域
- #異物混入
- #着工床面積
- #空調
- #結露
- #耐震工事
- #職場認証制度
- #自動倉庫
- #自動化
- #自動車運送事業者
- #衛生管理
- #補助金
- #規制緩和
- #調理器具
- #貸倉庫
- #軽油
- #適正流通ガイドライン
- #関西物流展
- #防災
- #防災用品
- #防爆構造
- #集中豪雨
- #電気代
- #電気代削減方法
- #静電気
- #静電気対策
- #非危険物
- #非接触
- #食品倉庫
- #食品物流
- #食品衛生法
もっと見る▼